Fixed Asset Audit
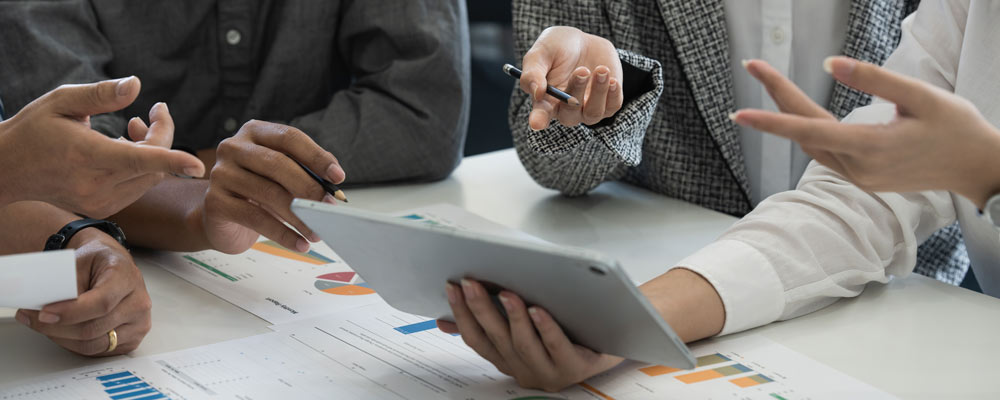
In many organizations, the internal control procedures require a complete fixed asset audit at regular intervals, usually three to five years. In far too many cases, compliance amounts to a wink and a nod between those responsible because it's common knowledge that such audits are all but impossible to be performed yielding meaningful results. Nonetheless, some action is needed. So, departmental reports are printed, sent to the field, returned to the auditors, spot-checked, and filed. Mission accomplished.
Sound familiar? The underlying weaknesses of this near futile exercise are both technical and procedural. Technical issues are most numerous:
- Accounting records include only capitalized assets so that some items in a class may be included and others not included based on a dollar limit in place when they were purchased. Confusing, at best, for field managers.
- Adding to the confusion is the practice of aggregating asset purchases for accounting purposes so those individual assets loose their identity.
- No basis or data exists to uniquely identify assets such as asset tag, bar code or serial number.
- Assets have not been tagged so the entire process relies on visual confirmation by the person performing the inventory.
These technical issues are aggravated by procedural weaknesses. Field personnel charged with performing the verification have little incentive to do so accurately; it is often viewed as one more task to be completed. No audit trail exists confirming that a field inspection occurred. As long as reported discrepancies are not material, little action results from all of the effort.
But those who truly understand the significant limitations of this approach are equally concerned that correcting them will be too time consuming, too costly or meet resistance from management. A well-designed asset management application can overcome those concerns. The strategy is this:
- Instead of the traditional inventory, conduct an accurate, detailed physical inventory and tag all assets with bar code or RFID tags.
- This should not cost much more than the traditional inventory and it need only be done once.
- Reconcile this field data to the accounting records to confirm assets found and those missing.
- Implement an asset tracking application to be maintained by line management that interfaces easily into the accounting system for capital assets.
- Insist that newly acquired assets be tagged and relevant information recorded upon receipt.
Once this effort is complete, the next audit simply amounts to scanning the asset tags at each location and updating the database. Then reports may be printed for assets found, transferred, not found and added during the inventory. Solid results with a complete audit trail at a fraction of the cost of traditional inventories.
Accurate, auditable results at a lower cost. How about a wink and a nod for that?